When you’re managing product quality for a consumer brand, it’s important to have a robust quality control plan in place to ensure that your products are well-made, safe for consumers, and compliant with all regulations. Many importers include third-party product inspections in their plans.
When an inspector goes to the factory, they need to have the right equipment to do the job well.
Here we talk about ten of the most important tools our inspectors use and why they use them. As a buyer, being aware of these will give you a deeper understanding of the inspection process and help you to ensure the highest quality products.
10 QC Tools Our Product Inspectors Frequently Use at the Factory
#1 Measuring Tape – Basic, yet essential, measuring tape allows the quality inspector to check the larger measurements of the outer carton, inner carton, and product. Made from metal, fiberglass, or plastic, any inspector worth their salt carries at least one of these on every trip to take measurements in either inches or centimeters.
#2 Calipers – When it comes to smaller, more precise measurements, calipers are king. They allow the inspector to measure small product components and features — for example, the thickness of a PVC flooring tile or the width of a small aluminum component.
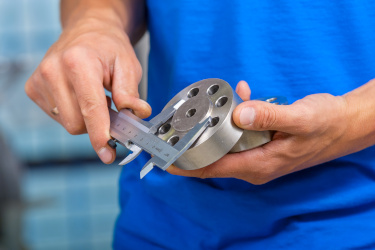
Calipers being used to measure the dimensions of a metal part
#4 Phone Camera – As the inspector takes all their measurements, verifies workmanship, and conducts on-site tests, they use their trusty phone camera to document every step. The photographs they take are added to the QC inspection report for the buyer to review.
#5 Defect Stickers – When dirt, scratches, or other visual defects are found, the inspector uses defect stickers to keep track of them and flag them in photos. This way, the defects are easy to spot as the buyer reviews their inspection report.
#6 Laptop – While on-site at the factory, the inspector always uses their laptop to enter the day’s inspection findings and upload photos. That way, the information can be converted into a polished inspection report for the buyer.
#7 Pantone Swatch – The colors on your products and packaging must match what you have specified. To verify that they do, the inspector sometimes uses a Pantone swatch in addition to your golden sample.
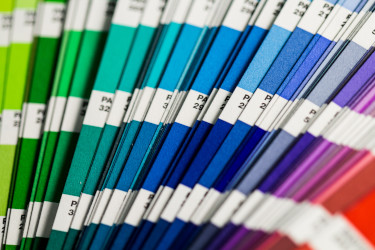
Pantone swatch for verifying color accuracy
#9 Barcode Reader – In the past, a physical scanner was required to check product barcodes and verify their accuracy. These days, the inspector uses an app on their mobile phone. Barcodes and labeling need to be clear, legible, and accurate — and this is an important part of your QC checklist.
#10 AQL Chart – While not necessarily a physical tool, the AQL chart is important because it determines how many units to inspect and how many defects are allowed before triggering a failed inspection. AQL sampling is a statistical tool that we use for every inspection we conduct at Insight Quality Services.
Will Your Products Pass or Fail Inspection?
Quality inspectors use these tools together with their knowledge, skills, and experience to determine whether the products in a shipment meet buyer requirements. Based on the number of defects they discover, they will give your shipment a pass, fail, or hold result.
What happens if your shipment fails?
When a shipment fails inspection, it can be frustrating. If you’re interested in learning about what to do when things go wrong with a supplier, we recommend downloading our Guide to Handling When Things Go Wrong.
Free Guide: What to do When Things Go Wrong
When a quality problem happens – and they will – how you approach the problem makes all the differences in successfully squelching it.
Learn how to deal with the problem at hand, see potential quality gaps throughout your supply chain, and take proactive measures to avoid future problems.
Great tools
Thank you, sir. For sharing such valuable information.