No one wants to import a product into the US and then find out that it has been deemed unsafe by the authorities—or worse—has actually injured someone.
Imagine that you purchase an order of adult sweatshirts from a manufacturer in Cambodia and have them shipped to America. You are seeing good sales and things are off to a positive start.
However, you are later shocked to find out that multiple consumers have called the CPSC (Consumer Product Safety Commission) and reported that your sweatshirts have caught on fire as they were cooking at home on their gas stoves.
It turns out that your product does not meet federal flammability standards and now needs to be recalled.
Situations like this are disastrous, but they can be avoided by conducting lab tests while your products are still in the country of manufacture.
In fact, you are often required by the CPSC to have what is called a “reasonable testing program” so that you can catch these issues before your products hit the market.
Table of Contents
What is a “Reasonable Testing Program?”
A reasonable testing program (RTP) is essentially a lab testing plan that you, as the importer, develop and follow. The goal of a testing program is to ensure compliance with any regulations that apply to your specific type of product.
As an importer selling products in the US, you are required to have your own RTP if you are:
- Selling non-children’s products for general use, and
- Selling a product that has any regulations that apply to it.
If you are selling children’s products, there are specific guidelines you must follow for testing and you must produce a Children’s Product Certificate. (See: CPSC website)
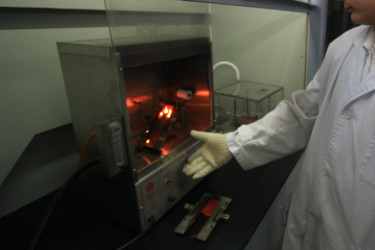
Flammability testing inside a laboratory
- Clothing textiles
- Bicycle helmets
- Antennas
- Lawnmowers
- Cellulose insulation
- Cigarette lighters
- Garage door operators, and
- Multipurpose lighters.
For other non-children’s consumer products there is no specific type of testing that needs to be performed, but your company management is required to have your own “reasonable” testing plan in writing.
You also need to issue a General Certificate of Conformity (GCC), which is shipped along with your products. (See: CPSC website)
How Do You Develop a Reasonable Testing Program?
If your product is in one of the categories listed above, look into the specific requirements for testing. If it is not, consider the following:
#1 What regulations apply to your product?
One tool that is helpful for determining this is the Regulatory Robot on the CPSC website. This tool is designed to provide guidance and to help you determine what regulations might apply.
Aside from the Regulatory Robot, consider consulting with an accredited test lab or a product compliance consultant.
#2 What is the right frequency for testing?
There is no one-size-fits-all answer to this question. But when determining a frequency, you should think about how much risk your product poses. For example, a soccer ball might not pose as much risk as a digital alarm clock, which uses electricity.
At a minimum, you should probably perform testing on an annual basis, but if there is a “material change” made to your product, you need to test again.
#3 Always Test When There is a “Material Change” to Your Product
A material change could include a design change, a change to a component, a manufacturing process change, or a change in raw materials.
Keep in mind, though, that if you change a component, you only need to retest that component. For example, if you make changes to the buttons on a jacket, you only need to retest the buttons.
If you switch manufacturers, of course, you will need to retest. Any time there is any kind of material change, retest.
The Most Important Thing is to Start Testing
If you don’t already have a testing plan in place, now is the time to create one.
By not testing, you are exposing yourself to significant liability and if something goes wrong, you could find yourself in the middle of expensive litigation.
Also, if you are making non-children’s products, it is not required that you test at a CPSC-accepted lab. However, we still recommend you do so. By using these labs, you can have more confidence in the result.
At Insight Quality, while we do not operate our own labs, we do offer testing management services and have resources we can provide for consultation on testing.
Also, we’ve put together a free lab testing guide that you can download if you are wondering how to get started.
Lab Testing: How to Get Started
As a consumer product importer, lab tests help you ensure that your products are compliant with regulations in the country of importation.
We’ve put together this guide to help you get started with lab testing so that you can make your products available for sale sooner rather than later. Avoid fines and customs issues by starting off on the right foot.
0 Comments