If you’ve hired a factory to produce consumer products — especially an overseas factory — you might want to verify product quality before they ship your order. That way, you can get a clear picture of how well-made the goods are before they make their long journey to your warehouse or distribution center. As such, you may be thinking about Final Random Inspections.
A Final Random Inspection is a product quality check that takes place after the factory has produced 100% of your order and it is at least 80% packaged. Many consumer product brands rely on this service to gain a presence at the factory and manage quality more effectively.
At Insight, we typically refer to these as Pre-Shipment Inspections since they occur before your products are shipped, but you’ll see both names used in the industry. And as a third-party inspection company, we’ve conducted tens of thousands of them and learned a thing or two along the way.
Here we discuss five things you must understand if you are considering Final Random Inspections.
Table of Contents
1) The Inspection Process
Let’s break down what happens before, during, and after your final random inspection.
Once you submit an inspection request, the inspector will verify the date with the factory. On that day, they’ll travel to the factory and sit down for a brief meeting with factory staff. Then, they’ll pull random cartons and product samples for inspection.
During the inspection, they’ll conduct special tests, check packaging and labeling, and run through all the items on your inspection checklist (discussed below). The checklist likely includes functional testing, barcode verification, physical requirements, and other checks relevant to your needs as a buyer.
After the inspection, they’ll review the results and put together an inspection report (also discussed below). It includes the photos they took, notes about any defective products, and a pass, fail, or hold result.
Learn More About the Inspection Process →
2) How AQL Sampling Works
Every time you hire an inspector, they will use a sampling method called Acceptance Quality Limit (AQL). This method helps them determine two things. First, it tells them how many pieces of your product they need to inspect. Second, it tells them how many defects are allowed before failing the inspection.
As a buyer, you must understand the sampling method well. This way, you can select the appropriate AQL and inspection levels for your situation. You also need to understand the types of defects (minor, major, and critical) and set the allowable percentage for each.
If you don’t fully understand the AQL methodology, you risk misinterpreting your inspection results, leading to excessive quality issues in the long run. It’s best to work collaboratively with your inspection service provider to get the best results, so be sure you have a firm grasp on this topic.
Learn More About AQL Sampling →
3) Getting the Inspection Checklist Right
How does your third-party inspector know what defects to look for when checking your products? The answer lies in your quality inspection checklist, which tells them what to measure, functions they need to test, barcodes to scan, and every other point of verification for the inspection.
As the buyer, you have the primary responsibility to ensure that your checklist covers every necessary aspect. However, you can also collaborate with your inspection provider to get their take on your checklist and provide their advice.
Also, keep in mind that any time you discover a new QC issue at your manufacturer, you should update this checklist so you can look for similar problems in the future. It’s a living document that should evolve over time.
Learn How to Create a Checklist →
4) Why Golden Samples are Essential
Your golden sample, also called an approval sample, is a perfectly-made version of your product from the initial sampling process. It represents what you expect your product to be like and serves as a standard you can compare to production goods.
When you begin working with a manufacturer, it’s crucial to develop golden samples. While your inspection service provider is at the factory, they can compare a golden sample to products from the production line.
Learn More About Golden Samples →
5) What is in Your Inspection Report
An inspection report is the end result of your final random inspection, and we send it to you after the work is done. It shows the results of each check performed and includes a collection of photos taken by the inspector. It allows you to get a clear idea of the condition of your products and packaging during inspection.
If you’d like to see a sample report, you can download one below. Or you can learn more about our pre-shipment inspection services.
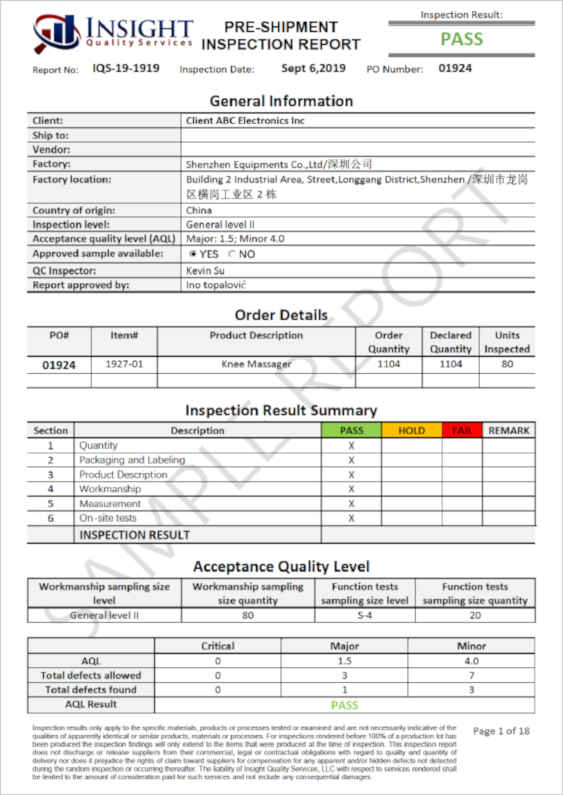
Download a Sample Inspection Report
Each time a product inspection is completed, we send you a report with the inspector’s findings. This inspection report gives you key information about the condition of the lot inspected.
It shows the results of each check performed and includes a collection of photos taken by the inspector. The photos allow you to see the condition of the products and packaging exactly as they looked during the inspection.
0 Comments