When manufacturing products overseas, it is vital to take all possible steps to ensure product quality. More than that, you must ensure that your products survive the journey from the factory to the port and then across the ocean to you.
Have you ever seen videos of airline workers handling luggage and tossing suitcases across the tarmac like giant rectangular baseballs?
If so, you know luggage is not always handled with the utmost care. And you may not realize it, but your cartons can receive similar treatment during their journey. As such, carton strength is a vital consideration.
A carton drop test is a procedure used to verify your carton can protect the products inside when being dropped multiple times and from different angles. Here is a video and, below that, seven things you need to know about it.
Table of Contents
#1 – ISTA 1A Lays Out the Accepted International Standards for Drop Tests
According to their website, the International Safe Transit Association (ISTA) is “an organization focused on the specific concerns of transport packaging.” With that focus in mind, the association has developed many protocols, including ISTA 1A.
ISTA 1A outlines acceptable procedures for several tests, including vertical shock tests, alternative incline tests, and alternative horizontal tests. It also outlines the accepted international standard for carton drop tests.
The carton drop standard outlines the various standard heights from which to drop the cartons and the ten different dropping angles.
#2 – Drop Test Height (See Chart) is Determined by Carton Weight
You may be curious about what height an inspector should drop the carton from during a product inspection. We determine the drop height based on the weight of a carton. For example, based on the table below, you can see that:
- A carton weighing less than 21 lbs (10 kg) would be dropped from a height of 30 inches (760 mm)
- A carton weighing between 100 lbs (45 kg) and 150 lbs (68 kg) would be dropped from a height of 8 inches (200 mm).
#3 – Cartons are Dropped 10 Times During Testing (See Diagram)
When performing a drop test, the carton is dropped on its most fragile corner, three of its edges, and six of its faces. In the diagram below, you can see how the faces, edges, and corner are identified.
In the table below you can see the details of the drop sequence. The carton will be dropped a total of 10 times.
#4 – After the Drop Test, Your Carton is Opened to Determine a Pass or Fail Result
Once the carton has been dropped from the appropriate height 10 different times, it will now be opened. The drop test is failed if any of the following is found.
- Damage to the export carton
- Damage to the product packages inside
- Scratches, dents, or other damage to products
- The products are not functioning as expected
If your cartons fail the test, it essentially means that they are not strong enough.
#5 – Burst Strength is Key to Passing Drop Tests
In order to ensure that your cartons are strong enough to pass a drop test, burst strength is one of the main considerations to keep in mind.
Burst strength is a measure of a box’s resistance to rupturing. It is measured in Pounds per Square Inch (PSI). At Insight, we recommend using cartons with a burst strength of 200 PSI for protection against rupture. Master cartons should have a seal specifying the burst strength and carton manufacturer, generally on the bottom side of the carton.
This should be sufficient to pass standard drop tests. While some factories have the necessary equipment to test and verify burst strength most do not. It would be necessary to send a sample carton to a testing lab if necessary to verify burst strength.
#6 – ISTA 1A Outlines More Than Just Drop Test Standards
In addition to carton drop tests, ISTA 1A outlines procedures for vertical shock tests, alternative incline tests, and alternative horizontal tests.
These tests are much less common and aren’t done by the average importer. They require the use of specialized equipment such as a shock test machine, incline impact tester and horizontal impact test system.
Drop tests, on the other hand, are fairly common.
#7 – Drop Tests Can be Done as Part of Your Pre-Shipment Inspection
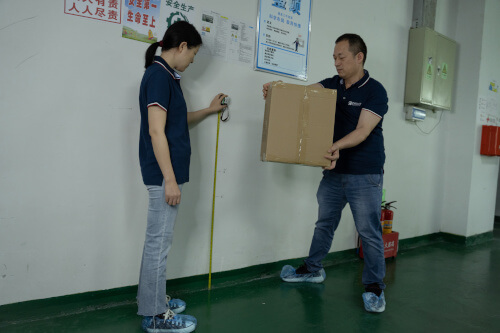
Insight inspectors conducting a carton drop test as part of an inspection
A carton drop test is most valuable when done on your first shipment and it can be performed as part of any pre-shipment inspection. By including it in your quality control checks, you can help ensure that the cartons you use are less likely to rupture and cause damage to your products and packaging.
By using high-burst-strength cartons capable of passing a drop test, you can be more confident that your products will make it to the country of importation unharmed.
If you are thinking of conducting a pre-shipment inspection, we recommend learning more about our services or reading the following guide.
Free Guide
How to Prepare for an Inspection
Are you thinking of hiring a third-party inspection company? If so, you need to be properly prepared. No one knows your product better than you do. So, make sure you give your service provider the information they need to ensure that your inspections are a success. Download this free guide to successfully preparing for your product inspections.
Note: This article was originally posted in November of 2018 and updated in April of 2025.
what is highest limit of drop test for heavy items.
Like book almirah, bed or bookshelf etc,
Generally 150 pounds is the limit for drop testing, which is the maximum weight in the drop test height chart above.
Below are the queries that I’m looking for –
1. Is this standard only applicable for packaging Items or single Item can be tested as per above mentioned table ?
2. Is is also applicable on Electronic hand held Items E.g. Neck Band, TWS, Earphone etc.
3. If this is not applicable on product then what exactly standard or table i can follow for the above mentioned items in No. 2 ?
Carton drop tests are not based on the number of items in the carton or the type of product. There could be 1 item, such as a portable generator, or 100 items, such as neck bands, in a master carton. The weight of the master carton will determine the drop height as specified in point #2.
How about for Plastic cabinets and drawers, as you can see this product is somehow bulky when it comes to size but do have lower weights. We always experience failure to drop test. Any recommendation?
If your items are breaking at the drop height that corresponds to the weight of the master carton then the next step would be to undertake a packaging design review. Packaging can be designed to ensure items arrive undamaged.
How about for items more than 68kg? is it applicable to any drop test ISTA height standard?
Generally, 68kg is the limit for drop testing as part of an inspection, which is the maximum weight in the drop test height chart above. To drop test heavier items requires specialized equipment (as outlined in ISTA 1B) and may need to be done in a specialized lab.
is this drop test suitable for glass bottle? If not, what other methods are recommeneded?
Hi Susan,
In some cases, you can drop test packaging for glass products. It’s essential to note that you should do the test on the outer carton, rather than on individual packages. As such, you need to invest in packaging that can withstand being dropped without breaking anything and come to an agreement with the factory about this. If your packaging requires a “Fragile” sticker, a drop test wouldn’t be appropriate. But if you’ve worked out an agreement with the factory to use packaging that can protect the glass products well enough, you can drop test them.
Can drop test be applied to products in glass bottles!?
Hi Samson,
Please see the reply to Susan, above.
is the drop test standard shown on #2 chart above the same for all ISTA #s ?
This article and chart above are specific to ISTA 1A.
Does this standard also applies with products that will be shipped to Amazon Fulfillment center? Do they only do the drop test on the carton and not on the product box itself?
Yes, this standard can be used for items shipped to Amazon. ISTA also has Member Performance Tests (ISTA 6 – xxx) that are created to reflect supply chain elements specific to Amazon’s needs and that have been determined by the ISTA Standards Council to be unique and therefore do not translate well to industry standardization. The tests may be completely original or may be modifications or variations of ISTA Procedures or Projects or other published and accepted tests.
UPS small box 13 x 11 x 2″ doesn’t have a burst strength certification label on them. How can I determine what that limit is? Or better yet, is there a rating
Also, UPS states that there needs to be a 2″ cushion of packing material protecting the item. How can you have 2″ on all sides of the item when the box is only 2″ thick?
The purpose of the ISTA test methods is to simulate the travel journey and effects on the packaging and products contained within. While we are not familiar with the packaging offered by UPS or their statements/requirements for goods that are shipped with them, it seems likely that packaging boxes they provide or sell would meet their own suggested burst strength requirements and/or suggestions.
Testing would be required to determine the burst strength of cartons without certification labels listing burst strength. If it is necessary to have 2” of cushioning material to adequately protect a carton’s contents then this would need to be factored in when determining the carton size necessary for your shipment.
Our Company is Manufacturing Fragile non sterile Medical Device packaged in 4 Cartoon boxes, Approx weight is 50-68 Kg, So is it compulsory to go for drop test.
Riya,
To determine if it’s compulsory, you would need to consult the rules and regulations for your product and market.
However, generally speaking, the purpose of drop tests is not to comply with regulations. We conduct these tests for our clients to help ensure their products can survive the shipping journey.
If you’re shipping sensitive equipment, conducting these tests might be a good idea, whether compulsory or not. That’s because, during transportation, cartons can get jostled around. And if a carton were to get dropped during loading or handling, you would want to be sure the carton you’ve chosen is strong enough to protect the goods inside. That is the primary purpose of these tests.
Keep in mind that you should only conduct drop tests if the factory has agreed to provide packaging that can withstand these tests.
If based on garment level, buyer have fixed below for the drop test, how can we do if “FAIL”? Thanks.
1. They have fixed cartons / packed of boxes request qlty and do not accept to add any protect cardboard inside the cartons.
2. They have fixed carton size but with tolerance.
3. They requested drop test to drop 10 times.
4. QA counted “FAIL” due to with deformed of cartons and packed of boxes at corner placement.
5. QA asked to no need re-do the drop test and file this for QA master file already.
If the cartons are exactly as specified by the buyer (or there is no specification for the cartons), you can reasonably expect that they might fail each time there is an inspection. A couple of thoughts…
1. Even if the result of the drop test is “FAIL,” the buyer can still decide to accept the shipment if they are okay with it.
2. In the future, if there is no change to the specification, you can reasonably expect that cartons might fail. As such, either:
(a) Work with the factory to determine a new specification for stronger cartons.
(b) Remove drop tests from the inspection checklist.
(c) As an inspector, we could use the HOLD remark instead of FAIL. This way, the buyer can learn the risk level for their packaging, but it doesn’t cause a failed inspection.
Hi,
Does this method hold true if we are importing the product packed in corrugated boxes?
Yes, this method is generally intended for corrugated boxes used for shipping.
Hello, what is the distance-weight relationship determined according to. Why is 10 kg thrown from 76 cm, is there a formulation for this?
Oktay,
The various drop heights used in the chart come from the ISTA1A standard, which was developed by the International Safe Transit Association (ISTA). Because the height-weight relationship is beyond the scope of this article, we recommend researching this standard to glean more information.
Thanks for this discussion.
I have a product that will be suspended by foam end caps and a center foam band in a 9″ x 9″ x 48″ hd box with total weight between 38lbs and 45lbs. The product itself is 6″ x 6″ x 44″.
The foam ends I use on another similiar product is: #1.7 LB PE Black Laminated End Cap with Chamfered Corners.
These will be shipped via UPS/FedEx Ground service.
What is the testing requirements for this?
What is the height for the drop test?
How many times does it get dropped?
Thanks a ton for your insight and guidance, Scott
Scott,
Per the ISTA 1A drop standards, the carton would either be dropped from 24 or 18 inches, depending on its final weight. If it weighs from 21 to 40 lbs, it’s 24 in. From 41 to 60 lbs, it’s 18 in.
Also per ISTA 1A, it is dropped 10 times and on various corners, edges, and carton faces.
Whether your packaging is designed to handle all this dropping is another question. Before deciding to conduct any drop testing, you should first discuss with your manufacturer to make your intention clear. Then you can determine whether your existing packaging can withstand drop tests. If not, you may want to consider alternative packaging and put your drop testing plan into effect.