Before your manufacturer begins production, they may need raw materials such as a specific grade of plastic or metal. However, your end product and business results can suffer if they don’t follow good procedures to ensure raw material quality.
Substandard materials can make your products more prone to breakage or perform inadequately, leading to problems later on, such as increased returns, one-star reviews, and customer complaints.
What practices should your manufacturer follow when inspecting raw materials? How can you verify they’re following them? This article will help you understand how to ensure raw materials meet acceptable standards so you can avoid quality disasters.
Table of Contents
How Should Your Manufacturer Handle Incoming Materials?
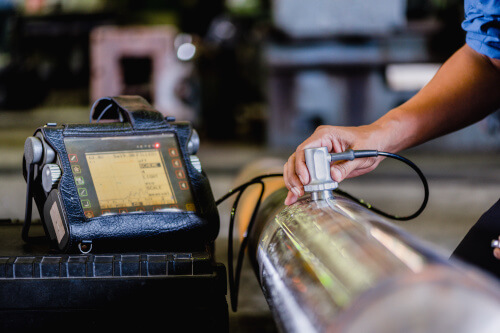
Ultrasonic test to detect imperfections in steel
Any factory you work with should have a well-defined Quality Management System. ASQ defines this as “A structured framework that defines and documents an organization’s processes, procedures, and responsibilities for achieving quality policies, practices, and objectives.”
With a QMS in place, they should be able to give you a step-by-step overview of their incoming material inspection procedure. Conducting raw material inspections typically involves four steps.
Step 1: Keep All New, Untested Material in a Separate Area
When they order a batch of raw materials and receive a shipment—whether it’s 304 stainless steel, 6061 aluminum, PET plastic, or something else—they should set the incoming raw materials aside in a specified area. They should stay in that receiving area until your supplier tests them.
Step 2: Conduct a Receiving Inspection to Test Raw Material
The manufacturer should check the material in the receiving area to ensure it meets the specified requirements. Some manufacturers use special equipment for material testing. For example, they might use an Optical Emission Spectrometer (OES), such as those made by Hitachi, to test metals. This device can identify the specific alloy used with high accuracy. Regardless, they should have some inspection process in place.
Step 3: Reject Any Material That Does Not Match Specifications
If the material does not meet specifications, it should be rejected. After discovering any non-conforming material, the inspector should set it aside and store it before sending it back. They should then follow up with the supplier to discuss the quality issues and determine the appropriate corrective action.
Step 4: Move Accepted Material to Pre-Production Storage
If a batch of material has been inspected and meets the specified criteria, the inspector can remove it from the receiving area. Then, they should send it to the pre-production storage area, where it can be used later for the manufacturing process.
Now that you know the steps your manufacturer should take as part of their incoming inspection procedure, what can you do as an importer or buyer to ensure material quality?
4 Ways to Ensure the Quality of Raw Materials
Verifying material quality can be tricky when working with a factory overseas. Here are some actions you can take to help ensure your manufacturer faithfully adheres to good practices and will provide the quality you expect.
1) Provide Material Specifications to the Factory
You can’t expect your supplier to use a specific steel grade or type of plastic unless you provide precise specifications. A lack of specifications is one of the major reasons importers need to scrap and rework products.
Provide your factory with product specifications that include all relevant details about your item, such as its size, shape, measurements, and colors—and, as we’re discussing here—its material and component details. That means not just specifying a material like ‘aluminum’ but a specific alloy such as 6061 or 6063.
A lack of precise specifications makes it much more challenging to hold the factory accountable, making it one of the primary drivers of quality fade.
2) Regularly Audit Your Supplier’s Quality System
Earlier, we discussed the processes a manufacturer should have in place, but how do you verify your supplier follows these practices? This is where factory audits come in.
An auditor travels to the factory to assess its quality management system, including incoming material quality control. They review the documented processes for raw material quality control and check the factory’s receiving inspection records to verify that they’ve consistently followed them.
Factory audits are essential when you’re considering a new supplier or have issues with an existing one and want to understand the problem better. Review our factory audit checklist example to learn more about the checks to perform.
If you need help conducting an audit, learn more about our factory audit services.
3) Conduct Lab Tests on High-Risk Raw Materials
Lab testing is an essential service that enables you to verify safety, regulatory compliance, or performance. You might be subject to various regulations depending on your product’s category.
For example, if you sell products in the US, you may need a General Certificate of Conformity (GCC) or Children’s Product Certificate (CPC). If you are selling products in California, they may need to comply with Cal Prop 65. Testing raw materials helps verify compliance with these requirements.
Not every batch of raw materials needs to be lab tested, but some are higher risk than others and may warrant more frequent testing. For example, incoming paint should be tested to ensure it is lead-free, and fabric should be tested to ensure it meets flammability and colorfastness requirements.
You can ask your supplier to provide a testing certificate for each batch to ensure they have verified its compliance. You can also periodically conduct your own tests with a testing lab to reduce the risk that comes from relying only on the supplier to authenticate their goods. If you need help, learn more about our lab testing services.
4) Conduct Raw Materials Inspections
Suppose you’re working with a new supplier or think your existing manufacturer might be cutting corners on incoming quality control. In that case, you can conduct a raw materials inspection yourself or hire a third party to help.
There are various types of inspection you can conduct at different manufacturing stages. Many importers know they can inspect the finished product after production, but some don’t realize they can inspect raw materials during pre-production.
You can send an inspector to the factory to verify that the raw materials received match the specifications you agreed to with your manufacturer. If you need help with this, learn more about our pre-production inspection service.
Also, to learn more about how to audit a factory, we recommend the following guide.
Free Guide
How to Prepare for a Factory Audit
A factory audit helps you assess a supplier's systems, capacity, workplace environment, or capabilities to ensure they meet your requirements as a buyer.
But which type of audit should you conduct, and which points should you cover on your checklist? In this free guide, you'll learn how to run an effective supplier assessment.
Note: This article was originally published in November of 2017 and was updated in April of 2021.
0 Comments