When you want to ensure the quality of your products, working with an inspection company in China can be a smart move. Many savvy buyers understand that conducting a quality inspection while goods are at the factory can help them catch issues early and avoid shipping low-quality products.
However, before you work with a China inspection service, there are certain things you need to know. Not understanding them can lead to suboptimal results from your QC efforts and receiving products that don’t meet your expectations.
Here we explain five mistakes to avoid as you think about working with a third-party inspection services provider. This advice will make the relationship with your China inspection company more productive so you can reap all the benefits of this service.
Table of Contents
Mistake #1: Over-Reliance on Your Service Provider
When going into any business relationship, it is essential to do so with eyes wide open. As such, you should understand what your service provider can do for you — and what they can’t.
For example, they can send a quality control inspector to your factory to perform all the various tests and checks on your QC checklist. They can’t, however, be expected to develop that checklist independently.
When it comes down to it, they are going to the manufacturer’s facility on your behalf. As such, you should have a clear idea of why they are there and be the one directing the activities they will perform. Otherwise, the inspection may not accomplish what you think it will. The following few points will help you avoid this over-reliance.
Mistake #2: Creating an Ineffective Inspection Checklist
As we’ve stated already, companies sometimes rely too much on their China product inspection services. As the buyer, ensuring that you have an effective checklist is primarily your responsibility.
Think about it this way — your product and its packaging are different from all the other products on the market. Your standards for quality may be different from your competitors. So your checklist should be unique to you, but how do you develop a good one? (See a QC checklist example)
The most important thing is to make it a collaborative effort between you and the service provider. While you understand your product and all its nuances better than anyone, your third-party inspection company may have extensive QC experience with products in your category.
To develop an effective checklist, it is vital that you:
- Come up with a well-defined list of defects to avoid.
- Choose the most appropriate AQL and inspection levels.
We will talk more about how to do so in the following points.
Mistake #3: Not Defining Defects Clearly Enough
Imagine that you are purchasing 1,000 kitchen countertops from a manufacturer and have partnered with an inspection company in China. Your inspector is measuring the countertops and notices several of them are around one centimeter longer than they should be. Then, he marks the length of the countertops as acceptable.
Did he make the right choice? The answer depends on how you have classified various types of defects. For example, you might decide that if a countertop is more than half a centimeter longer than your specified length, it is unsaleable. On the other hand, you might specify that a one-and-a-half-centimeter variance is satisfactory.
Defects are always classified as minor, major, or critical. Minor defects are slight deviations from your specifications that are still saleable. Major defects make the product unsaleable or likely to be returned. Critical defects are those that could cause injury to the consumer, such as splinters or a sharp pointy edge. You can learn more about this in our article on AQL defect classification.
Mistake #4: Choosing the Wrong AQL and Inspection Levels
When working with an inspection company in China, you must understand the AQL sampling methodology. AQL stands for ‘Acceptance Quality Limit.’ It is a statistical method for determining how many units to inspect and how many defects are allowable during your inspection.
For example, you might decide that over the course of many shipments, it is only acceptable for 2.5% of your products to have major defects that make them unsaleable. Or you might decide that only 1% of your products should have major defects. Keep in mind that defects are normal in any manufacturing process, so it is a question of deciding on a level that is appropriate for your brand.
Aside from the percentages of allowable defects (AQL levels), you should also consider your inspection levels. These represent the amount of confidence you need to have in the inspection. When you raise them, your QC partner will inspect more units, and when you decrease them, they check fewer units — which impacts your costs. Learn more about how to choose the right AQL and inspection levels.
Mistake #5: Thinking of Inspections as a Cure-All
Working with a China inspection service can be a great way to ensure that the quality of goods your factory produces meet your company’s standards. It is crucial, however, to realize that quality cannot be inspected into a product.
In other words, there are other more foundational aspects of quality management that you need to pay attention to as well. For example, the most basic one is your product’s design. If you want to sell a reliable product that consumers will be able to use for years, you need to think about the materials and components you use to make it and how they all work together.
An inspection can verify that a product meets your specifications, but what if your specifications are no good in the first place? Product quality starts with designs and specifications, then the manufacturing process and your suppliers come in. To ensure that a manufacturer is capable of producing your product well, you should conduct factory audits. Holding a supplier to a standard they can’t meet in the first place isn’t going to help you very much.
To ensure quality, start with design and specifications, build manufacturing relationships with partners that can meet your needs, and take steps to develop your suppliers. When you do, utilizing a quality control service in China will be more effective at helping you meet your goals.
Learn More About Insight Quality Services
Insight Quality Services is a US-based quality control and assurance company with offices in China. We can help you conduct pre-shipment inspections, supplier audits, and lab tests. Learn more about our China product inspection services or download a free sample inspection report. Feel free to reach out with any questions you have or to get a quote.
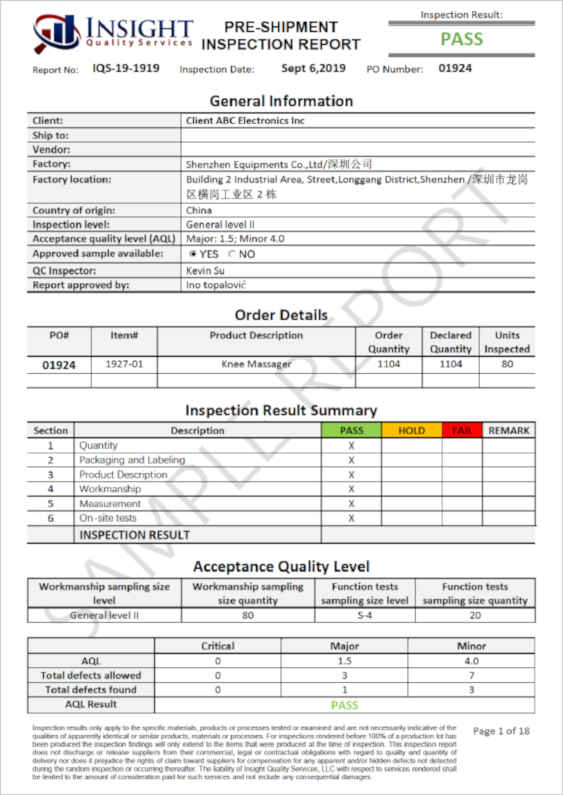
Download a Sample Inspection Report
Each time a product inspection is completed, we send you a report with the inspector’s findings. This inspection report gives you key information about the condition of the lot inspected.
It shows the results of each check performed and includes a collection of photos taken by the inspector. The photos allow you to see the condition of the products and packaging exactly as they looked during the inspection.
0 Comments