Are you planning to conduct inspections using the AQL sampling method? You may be aware that three types of defects — minor, major, and critical — play a role.
To conduct an effective inspection, you must understand these three defect types and develop a thorough defect list. Otherwise, you risk misinterpreting your inspection results and making your quality control efforts less effective.
Here, we discuss why defect classification is so important, define the three types of defects, and explain how to develop your defect list.
Table of Contents
Video Overview of the 3 Defect Types
In this video, we break down the differences between the three types of AQL defects and how to develop a defect list. For more information, continue reading on, below.
Why is Defect Classification Essential?
When you send an inspector to check a product for defects, specificity is critical to success.
Let’s say your product is a wooden standing desk. Your inspector checks a desk, and the surface measures 66.7 cm wide. However, according to your product specifications, it should measure exactly 66 cm wide.
They found a variance of 0.7 cm, so is the item acceptable? Well, that depends on how you’ve classified defects for your product.
The way you classify a 0.7 cm variance could mean the difference between a passed inspection and a failed inspection. You might decide that a 0.7 cm variance is perfectly acceptable. Alternatively, you might decide that it’s defective but still saleable (a minor defect) or defective and unsaleable (a major defect).
Different companies have different quality standards — a high-end brand might be less tolerant of inaccuracies, while a low-end one is more tolerant. Even within a product, some measurements and attributes need to be more accurate than others. As such, deciding on the most suitable standards for your situation is essential.
The 3 Types of Defects Used in AQL Inspections
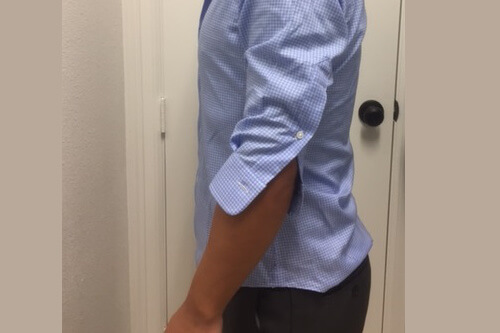
Read the following descriptions to decide whether this sleeve length is a minor, major, or critical defect.
Let’s define the three defect types and go over some examples.
#1 Minor Defects
A minor defect is one where the item deviates slightly from your specifications, but it’s still saleable and unlikely to trigger a return.
Let’s say your product is a 24-inch computer monitor with a quarter-inch scratch on the back. That small scratch might not be very noticeable and won’t affect a consumer’s experience of using the monitor, but it is still not ideal.
Another example of a minor defect would be a slight color variance, such as a stapler that is supposed to be cobalt blue but is more of an azure blue. The difference is only noticeable when you compare it side-by-side with your golden sample.
Any time you specify measurements, you must also set a specific tolerance. For example, you might decide that any variance between 0.3 and 0.8 cm is a minor defect. So, if a standing desk is supposed to be 66 cm wide but has a 0.7 variance, that would qualify as a minor defect.
#2 Major Defects
A major defect is one that makes your product unsaleable or likely to be returned by the consumer.
If you had a 24-inch monitor with a quarter-inch scratch on the front of the screen, it would likely affect the user’s experience. They might give you a poor review and return the item, hurting your brand reputation.
A stapler that says it’s cobalt blue on the box but is actually cherry red is a glaring mistake. And a lock with a key that doesn’t open it or a pair of skinny jeans labeled as relaxed fit will not go over well.
If you consider a variance between 0.3 and 0.8 cm to be a minor defect, anything over 0.8 becomes a major defect. So, a 0.9 cm variance on a 66 cm measurement would be outside your tolerance range and thus a major defect.
#3 Critical Defects
A critical defect is one that could cause injury to the consumer or even — in extreme cases — death.
For example, imagine a wooden picture frame with splinters, a phone with a battery that overheats during battery cycle tests, or a piece of furniture that topples during an incline test. These would likely be considered critical defects, resulting in an immediate failed inspection.
Also, any item with insects, blood, or hair inside the packaging is generally considered to have a critical defect. So, now that we’ve talked about the three types of defects, let’s discuss your defect list.
How to Develop a Defect List for Your Product
Every AQL inspection is run based on a quality inspection checklist, and every checklist is based on a list of potential defects the inspector should check for. You should never rely solely on an inspection services provider to develop these for you.
Instead, it’s best to collaborate with them by brainstorming your own minor, major, and critical defects and then seeking their input. This way, you can ensure that the checklist is tailored to your company’s needs and simultaneously leverages the quality control experts’ experience. If you’re planning to conduct third-party inspections, feel free to reach out to us, and we can provide our input.
Some Tips for Brainstorming Defects
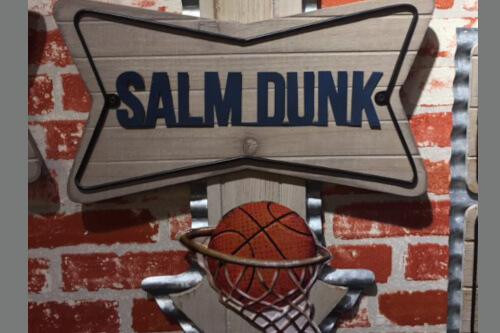
Follow these tips to make your defect list a salm… erm… slam dunk
The process of defect brainstorming will vary depending on whether it’s for a new product or one you’ve already sold before. Here are some places to look to help you begin the process.
- Return Data and Complaints: For items that you’ve sold before, you can look at negative reviews and the reasons for returns to gain insight into potential defects.
- Data From Similar Products: You can look at return and complaint data from your other products that are similar. Negative reviews of a competitor’s products can also give you insight into their customers’ issues.
- Product Specifications: Think about your product and its specifications. What should the product look like, and how is it supposed to function? With this in mind, consider what might go wrong.
- Sampling Process: Take a look at your samples. What issues or potential problems can you see? Compare your samples to their ideal specifications. What deviations do you note? Did you have any problems when you were under development?
- Testing Samples: Test your samples rigorously to see what issues develop. You can expect that similar problems might be found with products from mass manufacturing.
Once you’ve got a list of defects down on paper, consider how to classify them as minor, major, and critical. Put together any photos you can, share the defects with your third-party inspector, and see if they have any suggestions about what to add. You will now be more prepared to develop your inspection checklist and be on your way to conducting effective inspections.
If you’d like to learn more about our product inspection services, please get in touch with us. And if you’d like to get a complete overview of AQL sampling, we recommend downloading the guide below.
Free Guide
AQL Inspections 101: How They are Conducted
- Get a solid grasp of the AQL sampling method
- Understand the AQL tables and how to use them
- Work with your third-party inspectors more effectively
Note: This article was originally published in January of 2018 and was most recently updated in March of 2025
Can you please share articles on defect classification and defect prevention activities for software product development for ISO 9001:2015
Hi Ravindra,
Thanks for your question. However, Insight is focused on quality control and assurance for physical consumer products (e.g., furniture, apparel, electronic devices, etc.). So, unfortunately, we don’t have any information on software product development.
This sampling plan can be use to fruits, vegitables also.
Thank you for your comment. Fruit and vegetable quality control are outside our scope of business. However, we believe AQL is not typically used for this purpose. It would be best to consult with a company that provides services in this area.