In 2016, smartphone maker Samsung was forced to recall over 2.5 million Samsung Galaxy Note 7 smartphones after some gadgets started overheating and bursting into flames. This recall reportedly caused the company over $5 billion in losses.
A quick online search for product recalls will reveal hundreds of products that have been called back from the market due to defects or potential danger to the user. For importers, this is an absolute nightmare that can be the result of importing low-quality products from an overseas supplier.
To avoid such a disaster scenario, it is prudent to identify and mitigate quality issues early, before your products are shipped. This article introduces the steps you can take to ensure that you only receive high-quality products from your suppliers.
Table of Contents
What Happens if Your Manufacturer Has Quality Control Issues?
The bottom line is this — if your manufacturer has issues with quality control, you need to catch them early, or you will receive low-quality products. Failure to maintain quality standards can lead to costly product recalls, negative reviews on social media, product returns, and customer complaints that adversely affect your business.
While quality control issues can affect your bottom line, this is not the most significant danger. Safety defects, for instance, can be dangerous or even fatal to users. For example, in 2010, vehicle manufacturer Toyota recalled 3.8 million cars over gas pedals getting caught in faulty floor mats.
It is essential to arrest any QC problems as early as possible by implementing a reliable quality management system.
What is Quality Control, and Why Should You Put Your Own Measures in Place?
Quality control is the process of ensuring that your product is manufactured to specific preset quality standards. To ensure product quality, you should have a quality management system in place. Such a system ensures that all the appropriate processes and procedures for manufacturing are observed, maintained, and subjected to continuous improvement.
As an importer, you should put your own QC measures in place to guarantee that you deliver only the highest quality goods to your customers. Even if your supplier has sent you perfect samples, they might drop the ball during a future production run.
Having QC checks at different manufacturing stages will help identify issues as they occur. By identifying these issues early enough, you will ensure that your quality standards are maintained throughout production.
How to Identify QC Issues Before They Become a Problem
Sometimes suppliers make mistakes during the production process, which negatively affect the finished product. In theory, the factory’s internal QC should catch the issues before shipment. However, this doesn’t always happen, so many experienced importers put their own QC measures into place when dealing with low-cost country manufacturers.
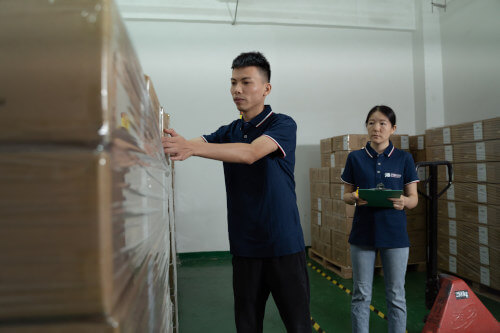
Insight Inspectors pulling cartons for a pre-shipment inspection
One of the most important measures you can take to identify issues is to conduct third-party product quality inspections while your goods are still at the factory. These inspections help you ensure that low-quality products do not make their way to your customers.
Quality inspections involve examining products during different stages of production to ensure that they meet the set standards. Pre-shipment inspections are the most common type of inspection. Conducted once at least 80% of your order is packaged, they help you catch any defects and assess overall product quality before your order ships.
Some importers conduct inspections at other manufacturing stages as well. For example, those that want to confirm the quality of the factory’s raw materials often conduct pre-production inspections. And importers producing high volumes on tight schedules often conduct during production inspections (DUPRO) to check product dimensions, appearance, and functionality early in the manufacturing process.
Such QC measures can help you catch the problems that occur. But some importers also take steps to prevent them from occurring in the first place.
How to Identify Quality Management Issues Before They Become QC Issues
While quality control measures can help you catch mistakes, big-picture quality assurance measures can help you prevent them before they happen. For more information about the difference between QA and QC, see our article on the topic. But generally, when we speak of QA, we are referring to factory audits.
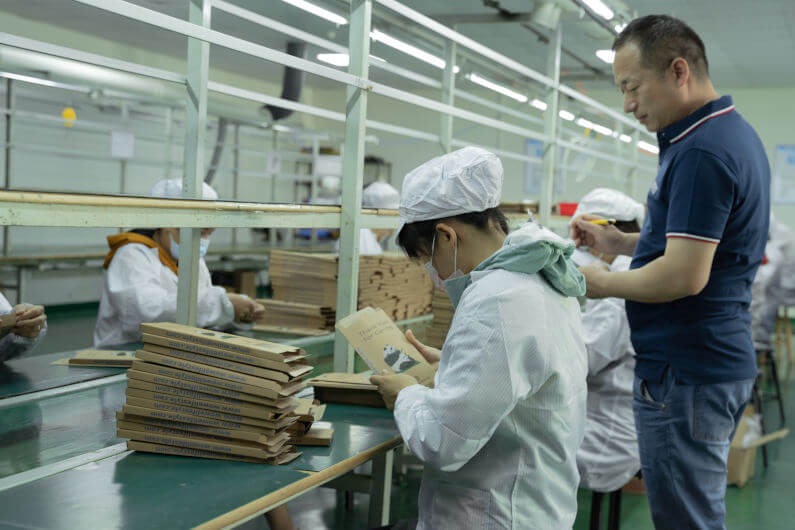
Insight auditor on-site at a factory
A factory audit involves visiting the factory either in person or through a third party to verify its capability to manufacture your order to the required standards. One aspect of a factory audit is to assess the factory’s quality management system. A quality management system is the sum of all procedures, practices, and processes used to ensure quality production.
The primary purpose of having such a system is to maintain consistency and provide feedback for continuous improvement. In addition, by conducting a factory audit, you will be able to assess the factory’s capacity and capability so that you can identify any specific weaknesses in their quality management system.
Factory audits are most helpful during the final stages of the sourcing process when deciding whether to work with a supplier. They are also beneficial when you have established long-term supplier relationships, and you want to strive for continuous improvement and verify that a supplier is still meeting your needs.
Now that we’ve covered the quality control and assurance measures you can take to ensure quality let’s recap our discussion.
Conclusion
As discussed, QC issues in the factory can result in low-quality goods. This, in turn, can lead to costly product recalls, customer complaints, product returns, and poor customer retention.
As an importer, you can take steps to mitigate these issues and avoid receiving low-quality products. One way you can do this is to conduct product inspections while your goods are still at the factory. And by auditing the factory’s quality management system, you can work to prevent them from happening.
If you are looking for reliable third-party factory audit and product inspection services, look no further than Insight Quality Services. To learn more about product inspections, download the Guide to Successfully Preparing for a Product Inspection here.
Free Guide: How to Prepare for an Inspection
Are you thinking of hiring a third-party inspection company? If so, you need to be properly prepared. No one knows your product better than you do. So, make sure you give your service provider the information they need to ensure that your inspections are a success.
0 Comments